Understanding GRP Enclosures: The Future of Durable Solutions
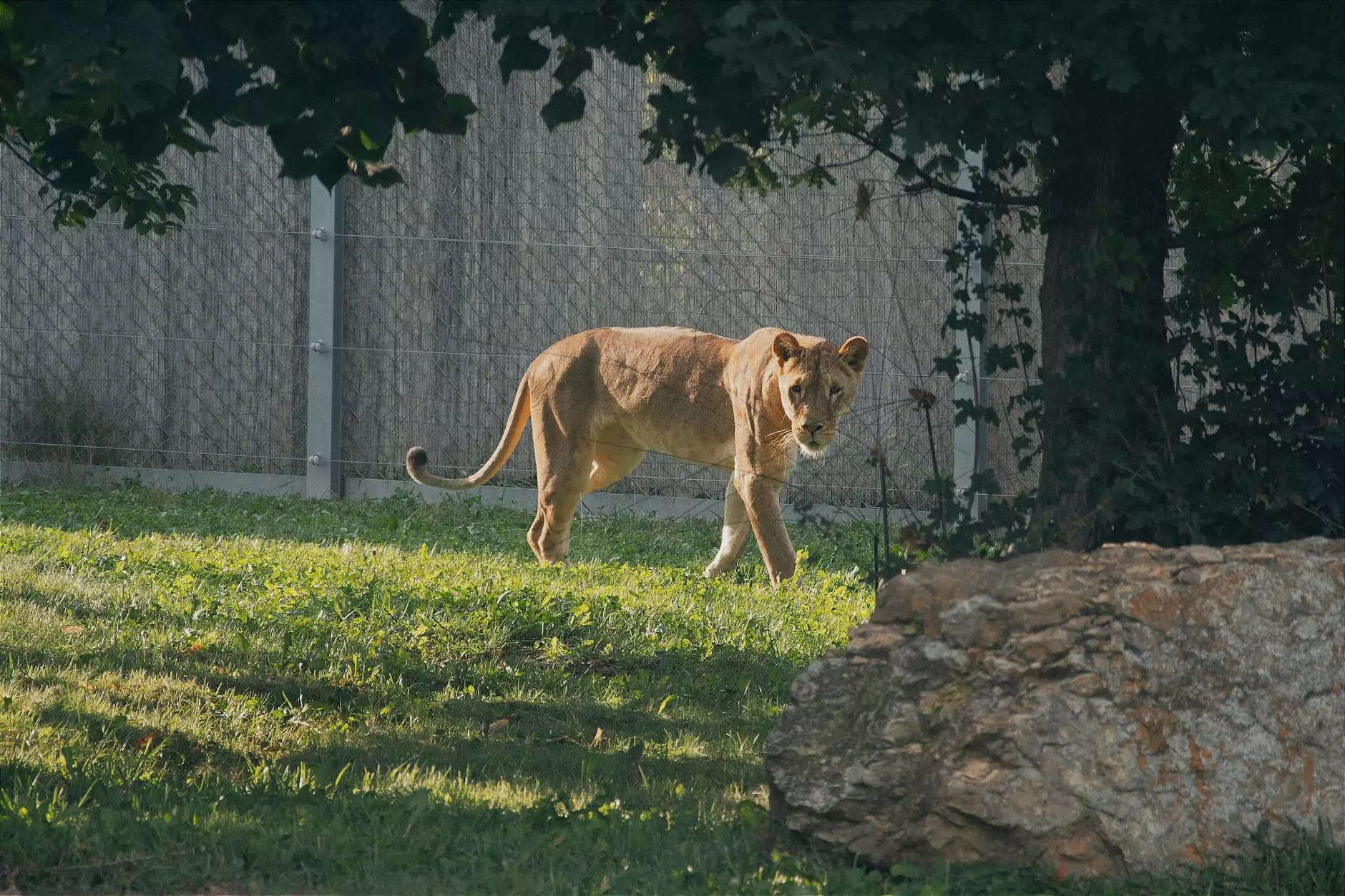
The term GRP enclosures, which stands for Glass Reinforced Plastic, refers to protective structures primarily made of a composite material that provides exceptional durability, lightweight properties, and resilience against harsh environmental conditions. These enclosures are becoming increasingly popular across various industries, including construction, telecommunications, and utilities, owing to their numerous advantages. This article delves into the composition, benefits, applications, and future of GRP enclosures.
1. What is GRP?
Glass Reinforced Plastic (GRP) is a composite material made by combining plastic with glass fibers. The infusion of glass fibers into the plastic matrix enhances the material’s strength and stiffness while maintaining its lightweight nature. GRP is renowned for its excellent corrosion resistance, ease of fabrication, and insulation properties, making it an ideal choice for various applications.
2. The Composition of GRP Enclosures
GRP enclosures consist of several components that contribute to their overall performance:
- Resin: Typically, unsaturated polyester or vinyl ester resins are used as the base material. These resins provide excellent durability and chemical resistance.
- Glass Fibers: The fibers provide structural integrity. They are often woven into mats or roving and are critical for enhancing the tensile and compressive strength of the enclosure.
- Additives: Various additives, such as UV stabilizers and color pigments, can be mixed with the resin to improve performance characteristics and aesthetic appeal.
3. Advantages of GRP Enclosures
GRP enclosures offer a plethora of advantages over traditional materials like metal or wood:
- Corrosion Resistance: GRP does not rust, rot, or corrode, making it perfect for outdoor applications and industries exposed to chemical substances.
- Lightweight: GRP enclosures are significantly lighter than metal counterparts, which reduces transportation costs and simplifies installation.
- Low Maintenance: Due to their non-corrosive properties, GRP enclosures require minimal upkeep over their lifetime.
- Customizability: GRP can be molded into various shapes and sizes, allowing for unique designs tailored to specific applications.
- Thermal and Acoustic Insulation: The properties of GRP provide effective thermal insulation, making it suitable for temperature-sensitive equipment. It also offers good acoustic insulation, which is beneficial in reducing noise pollution.
4. Applications of GRP Enclosures
The versatility of GRP enclosures allows them to be utilized in a range of industries:
4.1 Telecommunications
In the telecommunications sector, GRP enclosures are used to protect electronic equipment from environmental factors. They provide shelter for vital infrastructure such as antennas, satellite dishes, and server cabinets, ensuring that operations run smoothly without interference from the elements.
4.2 Utilities and Energy
Utility companies often rely on GRP enclosures for housing electrical connections, meters, and control equipment. Their durability ensures long-lasting protection against weather conditions and vandalism, allowing for uninterrupted service.
4.3 Construction Industry
In construction, GRP enclosures can be utilized for everything from portable toilets to site storage units and protective barriers. Their lightweight nature allows for easy relocation on construction sites while ensuring tools and equipment are safeguarded.
4.4 Marine Applications
The marine industry benefits significantly from GRP enclosures due to their excellent resistance to saltwater and humidity. They are commonly used in boat construction, storage boxes, and even sanitation systems on vessels.
4.5 Environmental Applications
Environmental services also employ GRP enclosures for waste management facilities, septic tanks, and containment systems. Their resistance to chemicals makes them suitable for handling hazardous substances.
5. Manufacturing Process of GRP Enclosures
The manufacturing of GRP enclosures typically involves several steps to ensure product quality:
- Design: A detailed design of the enclosure is created to meet specific dimensional and functional requirements.
- Mold Creation: Molds are constructed based on the design using various materials, including metal or durable plastic.
- Lay-up Process: In this step, layers of glass fiber and resin are applied in the mold. This process can be performed by hand lay-up or using automated methods such as spray-up and filament winding.
- Curing: Once the layers are applied, the material is left to cure, typically at room temperature or in an oven to ensure proper hardness and strength.
- Finishing: After curing, the finished enclosure is cleaned, inspected, and any additional features—such as doors, ventilation, and coatings—are applied.
6. Sustainability and Environmental Impact
As industries increasingly emphasize sustainability, GRP enclosures offer eco-friendly solutions. The materials used in their production can be recycled, and their longevity reduces the need for frequent replacements, minimizing waste. Furthermore, their lightweight nature translates to lower transportation emissions, contributing to a smaller carbon footprint.
7. Future Trends in GRP Enclosures
The future of GRP enclosures looks promising, as innovations continue to shape the industry. Key trends include:
- Smart Technology Integration: With the Internet of Things (IoT) becoming prevalent, GRP enclosures may integrate smart technology for monitoring environmental conditions or automated locking systems.
- Advanced Materials: Ongoing research may lead to the development of new composite materials that could enhance the properties of GRP, such as increased strength or improved fire resistance.
- Custom Fabrication: As industries demand more specific solutions, customization will play a significant role in the production of GRP enclosures, allowing for tailored designs to suit particular environments or requirements.
8. Choosing the Right GRP Enclosure for Your Needs
Selecting the appropriate GRP enclosure for a specific application involves considering several factors:
- Environmental Conditions: Consider exposure to harsh weather, humidity, or corrosive substances.
- Size and Shape: Determine the dimensions necessary to house the intended equipment effectively.
- Access Needs: Think about how often the enclosure will need to be accessed and whether additional features (like doors or ventilation) are required.
- Custom Requirements: Assess whether specialized features or designs are necessary for your application.
Conclusion
In summary, GRP enclosures are a modern solution combining durability, versatility, and sustainability. Their applications span various industries, demonstrating their critical role in protecting equipment and enhancing operational efficiencies. As technology continues to evolve, so too will the materials and designs used in GRP enclosures, paving the way for innovative and eco-friendly solutions. For businesses looking to enhance their infrastructure, investing in GRP enclosures offers a pathway to more reliable and sustainable operations.
For more information on GRP enclosures and to explore custom solutions for your needs, visit Celtic Composites.